ManufactPro™
ManufactPro™
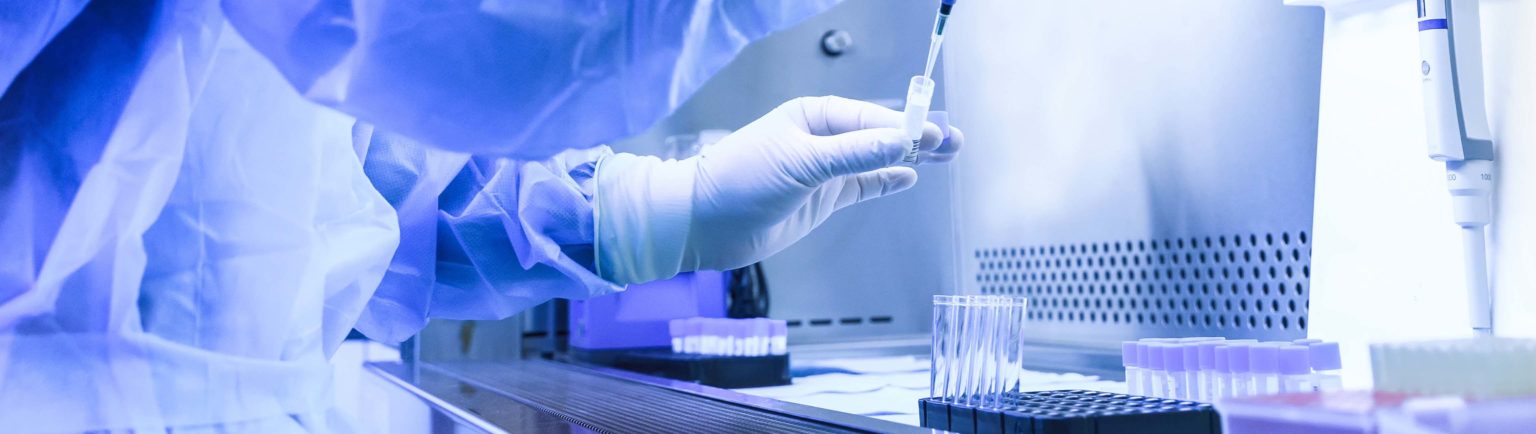
ManufactPro™ is an Integrated Documents, Materials, Parts and Quality Assurance database system focused on manufacturing of products and compliance with GMPs and ISO standards. Ideal for the start-up or small company that needs ISO and GMP compliance.
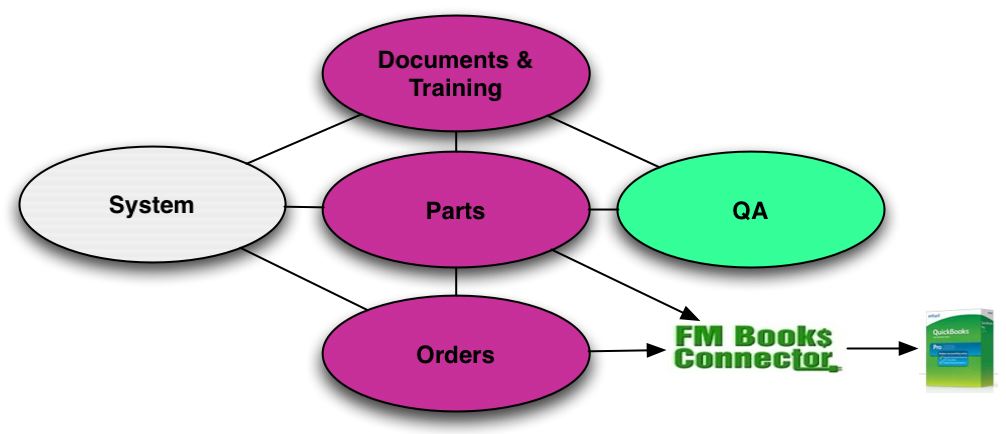
Documents and Training
Perfect for networked document control. Document numbers, training, change orders, and network opening of underlying documents. Keep your documents organized, get new document numbers, create change orders, review change history and open the electronic version of the document. Make the revision process quick and easy.
Documents allows you to keep your documents organized. You can get new document numbers, create change orders, track the revisions sent to outside and open the underlying electronic version of the document. Document records refer to actual pieces of paper or electronic files containing information. It is strongly recommended that all numbering schemes originate from this file: forms, SOPs, work instructions, part specifications, etc. Other database tables in the system are designed to refer to this database table when looking for information concerning revision level and revision date. To exploit the power of the database application, the document number should have a fixed pattern. This pattern is set in the preference file when your database is installed. Specific finds and sorts can be done using your custom prefix and suffix information. This pattern also will determine the next highest number in the sequence when creating a new document number. Other attributes of documents like release level, annual review and status are managed here.
Change Orders, (CO or DCO or ECO or ECN) (Change Order, Document Change Order) help you track and control changes for your company. The MFP change order makes change order creation easy. Change Orders are tracked by their status: open, close, cancel or void. Change Orders are automatically closed when the revision is changed in the Document Log. To avoid confusion, only one open Change Order is permitted for a document. This may be disabled by a preference setting. Problems can arise because the MFP does not know which change order closes first so manual data entry to correct the release level and next revision is necessary
Training links documents to persons and allows you, your managers and persons maintain their training records. Email listing training due and the last change order can be sent to each person. Individuals can record their own training with their electronic signature using MyTraining. The days of obsolete training records are past, training can be done as soon as the document is revised.
Each person has a set of documents that they are required to be trained and certified on. These different documents will require retraining at various points throughout the year and will appear on the work order. The work order can be printed either monthly or quarterly. The information from completed work orders is entered into the database to update the training records.
Employees can be Trained or Certified on documents. Training usually consists of reading the document. Certification usually consists of taking some sort of test. Training needs to occur on a regular basis and to be documented to meet ISO and GMP requirements.
Each document has a training frequency. This is a period of time in days, which when it expires, will prompt a training event. The training frequency field is located in the Doc Log.
Parts and Production
Supplier
Supplier tracks all the suppliers for your company. The suppliers can be used to create purchase orders and associated with parts for purchase orders and the forecaster.
Purchase Order
Purchase Orders help you quickly and easily create purchase orders for materials in the MFP system. PO’s for suppliers and materials not in the system can be created as well.
Lots
The MFP makes it easy to manage a controlled materials and assemblies via lot number. The lot number formats are customizable and you can have several different schemes.
The MFP system allows management of inventory by location. Find all the material in a location and to do a WIP-Work in Progress report for one or all locations
Parts
Parts is used to create, edit and manage parts, and assemblies. The part information is used to create part lots and the device history records (DHR) or batch records. Assemblies can have bills of materials, bills of documents, bills of specifications and drawings associated with them. Once a part is entered into the MFP, it can be used in another part or assembly.
The terms, DHR and Device History Record, can be changed in the preference file to your company’s convention. In this manual, batch records will be referred to as DHRs.
Forecaster
Forecaster is a great tool for planning future builds and to plan buying. You can run multiple “what ifs” and save old forecasts.
Quality Assurance
Quality Assurance tracks quality systems events for:
Corrective Action
Non-conforming
Special Requests or Deviations
Returned Material Authorizations
Complaints
The names for quality events differ from company to company and can be changed in the preference file.
Equipment
Equipment makes keeping track of calibration, preventive maintenance and repairs easy and efficient. The equipment database table stores and documents all your calibration records and preventive maintenance procedures.
Equipment uses the concepts of sets and work orders. Each piece of equipment can have a set of scheduled work associated with it. Each set item will generate a work order when it is due. One-time only work orders such as repairs or unscheduled maintenance can also be entered.
Equipment is designed to print out paper work orders and reports or to be used paperless with electronic signature.
Orders
Enter and ship orders. Track shipments by lot number. Manage finished goods inventory. Send order data to Quickbooks for accounting.
System
The Security system is similar to a Windows permissions based system. Each user has a log on username, password and set of permissions for which they can perform actions within the system.
• Easy log on processes.
• Easy set up and management of permissions
• Duplication of one permission set for another user.
• Forced expiration and deactivation of passwords.
• Administrative access to the security file.
• Three attempts for log on before system exits application.
The MFP system allows you to set specific permissions for a group and then assign the group to one or more users. Each user must be a member of a group to use the system.
Create groups first, then enter users and link to the permission group. A default group can be specified on the admin screen for new users after it has been created.